125y-500y 125X-500X PP PVC PVDF Structured Packing
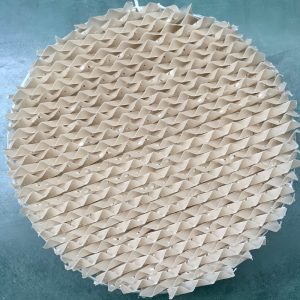
Type | Surface Area (m2/m3) | Void rate (%) | Pressure drop (Mpa/m) | Bulk weight (Kg/m3) | Factor (m/s (Kg/m3)0.5 |
SB-125Y | 125 | 98 | 200 | 45 | 3 |
SB-250Y | 250 | 97 | 300 | 60 | 2.6 |
SB-350Y | 350 | 94 | 200 | 80 | 2 |
SB-500Y | 500 | 92 | 300 | 130 | 1.8 |
SB-125X | 125 | 98 | 140 | 40 | 3.5 |
SB-250X | 250 | 97 | 180 | 55 | 2.8 |
SB-350X | 350 | 94 | 130 | 75 | 2.2 |
SB-500X | 500 | 92 | 180 | 120 | 2 |
PVDF (Polyvinylidene Fluoride) structured packing is a type of packing material used in various separation processes, especially in chemical and petrochemical industries. Here’s an overview of its features, applications, and benefits:
Characteristics
- Material: Made from PVDF, a highly durable and chemically resistant thermoplastic.
- Design: Typically features a structured design that maximizes surface area and facilitates efficient gas-liquid contact.
- Corrosion Resistance: Excellent resistance to a wide range of chemicals, making it suitable for aggressive environments.
Applications
- Distillation: Used in distillation columns to separate components based on boiling points effectively.
- Absorption: Effective in processes where gases are absorbed into liquids, such as in scrubbers and gas treatment systems.
- Stripping: Utilized in stripping columns to recover solvents or valuable components from mixtures.
Benefits
- High Efficiency: The structured design allows for enhanced mass transfer and reduced pressure drop, improving overall process efficiency.
- Durability: PVDF’s resistance to chemicals and high temperatures ensures long operational life.
- Lightweight: Easier to handle and install compared to traditional packing materials.
- Reduced Fouling: The design minimizes the chances of fouling, maintaining performance over time.