Ceramic Corrugated plate packing
Owing to ceramic surface has good hydrophilic, it can enlarge to gas-liquid contacting surface area. Meanwhile, ceramic surface’s microporous structure also improve wettability and generate extremely thin liquid film. Turbulent liquid flow and tortuous vapor flow passages promote mixing of liquid and vapor with a low pressure drop. This is why ceramic Corrugated plate packing has same mass transfer efficiency same as metal packing. Furthermore, Resistant to corrosion and high temperature performance is excellent than other material packing.
In addition, ceramic excellent corrosion resistance makes Ceramic Corrugated plate packing more suitable for sulfuric acid absorption, the nitrate concentration,gas purification and so on. Ceramic high thermal stability make its operating temperature exceeds 1000 ℃.
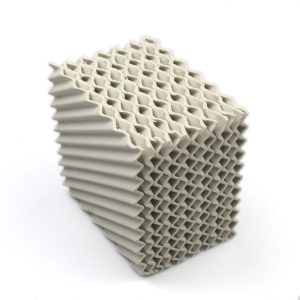
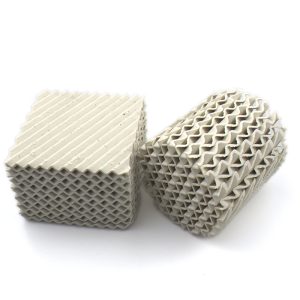
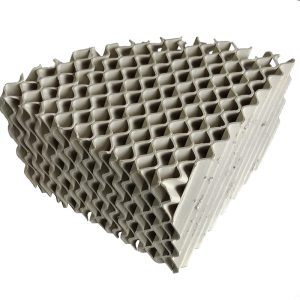
Technical Parameter
Type/ | Surface area m²/m³ | Buld Density Kg/m³ | Void Ratio/ % | Obl Angle/ ℃ | Pressure drop/ mmHg/m | Theo.Plate m-1 | Hydraulic Dia. mm |
250Y | 250 | 420 | 80 | 45 | 2 | 2.5 | 12 |
350Y | 350 | 470 | 78 | 45 | 2.5 | 2.8 | 10 |
400Y | 400 | 500 | 75 | 45 | 3 | 3 | 8 |
450Y | 450 | 520 | 72 | 45 | 4 | 4 | 7 |
550Y | 550 | 620 | 74 | 45 | 5.5 | 5-6 | 6 |
700Y | 700 | 650 | 72 | 45 | 6 | 7 | 5 |
250X | 250 | 380 | 80 | 30 | 2.5 | 2.3 | 12 |
350X | 350 | 450 | 78 | 30 | 3 | 2.5 | 10 |
400X | 350 | 480 | 75 | 30 | 4 | 2.8 | 8 |
450X | 450 | 500 | 72 | 30 | 4.5 | 3-4 | 7 |
500X | 500 | 620 | 74 | 30 | 5.5 | 5-6 | 6 |
700X | 700 | 650 | 72 | 30 | 7 | 7 | 5 |
Ceramic Corrugated plate packing
The corrugated plates are typically made of ceramic materials such as alumina, porcelain, or ceramic-based composites. These materials provide excellent chemical resistance, high mechanical strength, and thermal stability, making them suitable for demanding applications involving corrosive or high-temperature environments.
The design of ceramic corrugated plate packing allows for increased surface area compared to traditional random packing, which enhances mass transfer efficiency. The corrugated structure provides additional surface area and promotes the formation of thin liquid films, facilitating intimate contact between the gas and liquid phases. This leads to improved separation and absorption efficiency.
Ceramic corrugated plate packing offers several advantages over other types of structured packing. These include:
High capacity: The large surface area provided by the corrugated plates allows for efficient mass transfer, making it suitable for applications that require high separation efficiency.
Enhanced fouling resistance: Ceramic materials are resistant to fouling, scaling, and corrosion, resulting in longer service life and reduced maintenance requirements.
Thermal stability: Ceramic packing can withstand high operating temperatures, making it suitable for applications involving heat-sensitive compounds or elevated process temperatures.
Chemical compatibility: Ceramic materials are chemically inert and compatible with a wide range of corrosive chemicals, acids, and solvents.
Lower pressure drop: Compared to some other types of structured packing, ceramic corrugated plate packing typically offers lower pressure drop, reducing energy consumption and operating costs.
Trade Details
Related Trade Information | |
HS Code | 6914100000 |
Package | 1: Two Super sacks on Fumigation Pallet 2: 100L plastic woven bag on Fumigation Pallet 3: 500*500*500 mm carton on Fumigation Pallet 4: Upon your requirement |
Process Method | High temperature firing |
Material | Al2O. SiO2,Fe2O3 and so on |
Typical Application | 1.Sulfuric Acid Plant 2.Regenerative Thermal Oxidizers 3. Chlorine Cooling and Drying Towers 4. Bromine and Hydrochloric Acid Plant 5. Liquid Organic Waste Disposal Coolers and Scrubbers 6. Natural Gas Treating and Dehydration units 7. Purification of Aqueous Organic Acids. |
Production time | 7 days against one 20GP container loading quantity |
Executive standard | GB/T 18749-2002 or refer to your detailed requirement |
Sample | Free samples within 500 Grams |
Other | Accept EPC turnkey,OEM/OEM,Mold Customization,Installation&Guidance,Test, Entrusted design service etc. |
Typical Application
1. Sulfuric Acid Plant
2. Regenerative Thermal Oxidizers
3. Chlorine Cooling and Drying Towers
4. Bromine and Hydrochloric Acid Plant
5. Liquid Organic Waste Disposal Coolers and Scrubbers
6. Natural Gas Treating and Dehydration units
7. Purification of Aqueous Organic Acids.
Feature
1: Excellent surface wetting ability, larger mass transfer area, and higher separation efficiency, 2:High compressive strength;
2: Available specific surface area between 64m²/m³ and 500m²/m³;
3: Little magnifying effect;
4: More fields/conditions to be applicable.